La mirada que tenemos los que estamos caminando las empresas de alimentos hace muchísimos años – en mi caso más de 25 – es que, independientemente del país, de la cultura, y del idioma, siempre en calidad y producción estamos un paso por detrás.
¿A qué me refiero? Que se suele ver una desconexión entre el personal de línea; los procesos y los objetivos inmediatos de producción. Este escenario se intensifica aun más, y se pone de manifiesto cuando tenemos grandes líneas de producción con muchos operarios. Y se evidencia si los operarios trabajan con pobre cultura de inocuidad alimentaria donde: “Si no me corresponde realizar; no lo hago”.
Con la digitalización eso se resuelve en un click.
Ha sido; y sigue siendo muy lento el avance hacia la digitalización de procesos e integración de sistemas en la industria alimentaria. Esto genera que haya personal muy valioso, como de gestión de calidad o en producción “perdiendo” horas en tareas rutinarias que, al digitalizarlas, se pueden reducir en un 70% de tiempo. Un claro ejemplo son las inspecciones de material quebradizo en instalaciones, o las revisiones pre-operacionales de línea. Se requiere mucho tiempo y mucho esfuerzo de este personal muy calificado que tiene que estar mirando y contando, en una sala de 5000 m2 con más de 100 dispositivos de potenciales de material quebradizo y plásticos duros. Con la digitalización se logra tener este recurso liberado: todo ese personal competente tiene disponible este tiempo para poder trabajar en mejora continua.
Además de esta inversión de tiempo diario en estas tareas, al tener la mirada en un documento en papel a la vez, hace perder la mirada de “Big picture”. Por ejemplo, si necesitamos entender los datos a lo largo del semestre de una variable, como podría ser el resultado del monitoreo microbiológico ambiental de una zona de alto riesgo. Los datos podrían estar ajustándose a los valores que hemos fijado como límites aceptables, pero sólo el gráfico con tendencias, y alarmas tempranas nos dará una ventaja para poder actuar a tiempo en una zona que podría estar acercándose a estar fuera de control. Este sería el caso de tener varios puntos consecutivos que aumentan o disminuyen regularmente, y en este caso, hay un deterioro de la confiabilidad y/o la precisión y hay un sesgo.
La gestión de la trazabilidad es el primer elemento del sistema de gestión donde se pueden ver evidencias del efecto en la rapidez con la que se resuelve en una empresa que está digitalizada. Con la implementación de un software se optimiza el proceso, y se rentabiliza la inversión ya que se elimina el doble trabajo, se reduce el riesgo de errores humanos y siempre se logra estar actualizado.
De esta forma, se obtiene una nueva forma de trabajar para la fábrica ya que pasamos de procesos con toma de datos manual en papel; a una fábrica que está funcionando en un estado óptimo, reduciendo también los problemas por errores de tipeo en la documentación; o de dobles tareas o de tareas que no se hacen.
En otra escala del organigrama de la empresa; la gerencia necesita tener el reporting y no puede estar viendo el dato individual diario; sino que tiene que poder analizar el comportamiento de los indicadores claves de proceso dentro de un marco estadístico.
También hay ventajas para los auditores; ya que es una mirada mucho más fácil para poder entender el proceso. Recordar que durante una auditoría de certificación, de cliente, interna o de las autoridades sanitarias; en cualquier caso; en dos o tres días el auditor tiene que analizar y verificar lo que la empresa ha estado trabajando durante todo el año. Si el auditado no se sabe explicar bien o si la muestra de datos que se enseña durante la auditoría no es suficientemente significativa, se podrían sacar conclusiones erróneas. Si el sistema está digitalizado, el auditor ya tiene el “Big picture”; puede ver gráficos y puede sacar conclusiones con mayor peso estadístico.
Finalmente, cuando estamos implementando un software de procesos en una industria alimentaria, la ventaja evidente es tener la información en un vistazo: se entiende qué se ha hecho y qué está pendiente, con recordatorios automáticos constantes tanto de las acciones preventivas y las correctivas.
Además, hay un aprendizaje propio porque se evidencia la acción preventiva que ha sido la más eficaz para resolver las desviaciones de planta. Y esto también se extiende a la gestión de las medidas de control de un peligro significativo: como un desvío de un límite crítico en un PCC. Inmediatamente todos los responsables directos se notifican para poder actuar de manera temprana y ágil con la corrección y evitar que salga producto al mercado no inocuo. De esta manera aseguramos que se actúa con debida diligencia siempre.
Para conocer más sobre el tema los invitamos a participar del
Curso Online «Documentos de los Sistemas de Gestión de Inocuidad».
Autora:
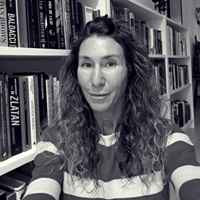
Leila Burin.
Coordinadora Académica de Portal de Inocuidad.
PhD en Ciencias Químicas, Universidad de Buenos Aires, 2001 y Lic. en Ciencias Biológicas, Universidad de Buenos Aires.
2010 hasta la fecha: auditora GFSI: Esquemas: IFS, BRCGS, ISO 22 000, FSSC 22000, y esquemas privados, como SQMS (Mac Donalds) con base en España.
1997 hasta la fecha: QualyFoods S.A. como Directora. Digitalización de procesos: Q-Chess mobile y asesoramiento en inocuidad alimentaria. Capacitadora reconocida: HACCP Alliance Lead Instructor y BRCGS ATP (2019/2022).
2022 hasta la fecha: representante ENFIT en España.
Portal de Inocuidad © Se prohíbe la reproducción total o parcial de los contenidos sin citar su fuente o solicitar autorización.
Aquí pueden dejarnos sus comentarios