Uno de los grandes retos en la Industria de Alimentos es la sensación de estar siempre un paso por detrás, y tener una desconexión entre personal, procesos y objetivos. Nos encontramos que nos falta poder ver y entender “the big picture”; es decir, al estar tan concentrados gestionando los datos individuales, nos volvemos ciegos ante los datos integrados, con un análisis de tendencias, o cualquier otra herramienta de control estadístico de proceso. Eso genera la incapacidad de poder actuar de manera preventiva en casos clave, y los impactos vienen en forma de no conformidades en auditorías de clientes, de Autoridades Sanitarias, o de Certificación de una Norma.
Para ello la Industria de Alimentos se va sumando, de a poco, a la digitalización de los procesos, y han surgido cientos de soluciones informáticas. El problema es que no todas están a “la altura” de la complejidad de las Industrias de Alimentos. Por ello, en este artículo me gustaría compartir, luego de estos últimos 7 años de “transformación digital”, mi experiencia:
- Softwares ya existentes en planta (de contabilidad, p.e.) que los han tratado de modelizar según los registros de proceso: han fracasado porque el diseño inicial, el código de programación no soporta las nuevas variables que la empresa necesita.
- Software nuevos, hechos “en casa” por alguna empresa sin experiencia alguna: han fracasado por falta de seguimiento del proyecto inicial, declarándose incapaces de lograr los objetivos que necesita la empresa
- Softwares nuevos, hechos por una empresa: pero delegando el 100% del trabajo de implementación a una sola persona en planta, que ya tiene otras funciones (Calidad, Producción, Mantenimiento).
- Softwares nuevos, hechos por una empresa, inicialmente económicos: pero a medida que la empresa necesita más recursos del mismo, se encarece de manera tal que ya no es viable la inversión aprobada inicial.
- Softwares nuevos, hechos por una empresa: sin embargo ésta no tiene experiencia en la Industria Alimentaria, y conlleva un tiempo extra no considerado inicialmente en el proyecto, agotando la capacidad interna y haciendo el efecto contrario de lo deseado por tener que explicar lo básico del sector.
Los síntomas descritos son la consecuencia de no haber hecho un buen análisis de inversión. Es decir, cuando falta de estudio de rentabilidad previa al proyecto a implementar; y no se han considerado los efectos para un proyecto integral, ya que hay dinero para ganar. La forma de medirlo no es cuánto se va a gastar, sino cuánto se va a ganar.
Por eso, nosotros consideramos que el mejor software para la gestión de los procesos en la planta es Q-Chess; es decir para la automatización y digitalización de datos que se generan en el proceso.
Llámenos o escríbanos para conocerlo.
Representantes en España Para Q-Chess:
Teléfono: +34 91 514 41 01
Email: info@qualyfoods.com
Autora
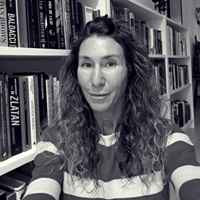
Leila Burin.
Coordinadora Académica de Portal de Inocuidad.
PhD en Ciencias Químicas, Universidad de Buenos Aires, 2001 y Lic. en Ciencias Biológicas, Universidad de Buenos Aires.
2010 hasta la fecha: auditora GFSI: Esquemas: IFS, BRCGS, ISO 22 000, FSSC 22000, y esquemas privados, como SQMS (Mac Donalds) con base en España.
1997 hasta la fecha: QualyFoods S.A. como Directora. Digitalización de procesos: Q-Chess mobile y asesoramiento en inocuidad alimentaria. Capacitadora reconocida: HACCP Alliance Lead Instructor y BRCGS ATP (2019/2022).
2022 hasta la fecha: representante ENFIT en España.
Portal de Inocuidad © Se prohíbe la reproducción total o parcial de los contenidos sin citar su fuente o solicitar autorización.
Aquí pueden dejarnos sus comentarios