Es de vital importancia para la industria de alimentos que el aire comprimido sea de la calidad adecuada. Si el aire que contiene contaminación entra en contacto con el producto final, materas primas, productos en proceso, superficies de contacto directo; los costos de rechazo pueden volverse rápidamente inaceptablemente altos.
Vapor de agua:
El aire de la atmósfera siempre contiene humedad en forma de vapor de agua, y si se incluye algo de vapor de agua en el aire comprimido puede causar problemas. Los ejemplos incluyen:
- altos costos de mantenimiento,
- vida útil más corta y rendimiento deteriorado,
- alta tasa de rechazo con pintura en aerosol e inyección de plástico,
- aumento de fugas,
- perturbaciones en el sistema de control e instrumentos,
- vida útil más corta para el sistema de tuberías debido a la corrosión y más costo de instalación.
El agua se puede separar mediante accesorios: post-enfriadores, separadores de condensación, secadores frigoríficos y secadores de adsorción. Un compresor que trabaja con una sobrepresión de 7 bar comprime el aire a 7/8 de su volumen. Esto también reduce la capacidad del aire para retener el vapor de agua en 7/8. La cantidad de agua que se libera es considerable. Por ejemplo, un compresor de 100 kW que aspira aire a 20 ° C y una humedad relativa del 60% emitirá aproximadamente 85 litros de agua durante un turno de 8 horas. En consecuencia, la cantidad de agua que se separará depende del área de aplicación del aire comprimido. Esto, a su vez, determina qué combinación de enfriadores y secadores es adecuada.
Las fugas también son una fuente de contaminación por vapor de agua. Siempre que la presión cae, crea una succión alrededor del área de la fuga que empuja el aire ambiental hacia el sistema. Si la fuga se produce después del secador o la filtración, puede provocar una contaminación por vapor de agua que afecte la calidad del aire.
Aceite en aire comprimido:
La cantidad de aceite en el aire comprimido depende de varios factores, incluido el tipo de máquina, el diseño, la antigüedad y el estado. Hay dos tipos principales de diseño de compresores: los que funcionan con lubricante en la cámara de compresión y los que funcionan sin lubricante. En los compresores lubricados, el aceite está involucrado en el proceso de compresión y también está incluido en el aire comprimido (total o parcialmente). Sin embargo, en los compresores de pistón y tornillo lubricados modernos, la cantidad de aceite es muy limitada. Por ejemplo, en un compresor de tornillo con inyección de aceite, el contenido de aceite en el aire es inferior a 3 mg / m3 a 20 ° C. El contenido de aceite se puede reducir aún más mediante el uso de filtros de varias etapas. Si se elige esta solución, es importante considerar las limitaciones de calidad, los riesgos y los costos de energía involucrados.
Los disolventes de proceso y las soluciones de limpieza pueden ser otra fuente de vapores de aceite en el aire que aparecen con bastante frecuencia.
Microorganismos en aire comprimido:
Más del 80% de las partículas que contaminan el aire comprimido tienen un tamaño inferior a 2 µm y, por lo tanto, pueden pasar fácilmente a través del filtro de entrada del compresor. Desde ese punto, las partículas se esparcen por todo el sistema de tuberías y se mezclan con el agua y los residuos de aceite y los depósitos de las tuberías. Esto puede resultar en el crecimiento de microorganismos. Un filtro colocado directamente después del compresor puede eliminar estos riesgos.
Sin embargo, para tener aire comprimido puro, el crecimiento de bacterias después del filtro debe mantenerse completamente bajo control. La situación se complica aún más, ya que los gases y aerosoles pueden concentrarse en gotitas (mediante concentración o carga eléctrica) incluso después de pasar varios filtros. Los microorganismos pueden germinar a través de las paredes del filtro y, por lo tanto, existen en las mismas concentraciones en los lados de entrada y salida del filtro.
El aceite y otros contaminantes actúan como nutrientes y permiten que prosperen los microorganismos. El tratamiento más eficaz consiste en secar el aire a una humedad relativa <40%. Esto se puede lograr utilizando cualquier tipo de secador, y colocar un filtro estéril en el sistema. El filtro estéril debe colocarse en una carcasa de filtro que permita la esterilización con vapor in situ o que se pueda abrir fácilmente. La esterilización debe realizarse con frecuencia para mantener una buena calidad del aire.
La norma ISO 8573-1 clasifica los contaminantes del aire en tres categorías:
- Partículas sólidas: minúsculas porciones de materia como el polvo o el óxido.
- Agua: el aire atmosférico contiene vapor de agua y, cuando se comprime, su concentración aumenta. Es inevitable que esto suceda, pero podemos secar el aire comprimido para minimizar los estragos del agua en las máquinas, tuberías, depósitos y herramientas.
- Aceite: en los compresores lubricados, el aceite puede contaminar, en mayor o menor medida, el caudal de aire comprimido y producir desperfectos (grumos, burbujas, imperfecciones…).
Dentro de estas categorías, la concentración de contaminantes se organiza en seis niveles, siendo la clase 0 la más pura de todas y la clase 6, la menos. La pureza del aire comprimido se expresa de la siguiente manera: ISO 8573-1 : 2010 [A: B: C]. “A” es la clase requerida de partículas sólidas; “B” de humedad y agua; y “C” de aceite en cualquiera de sus formas (líquido, aerosol y vapor).
Por ejemplo, si identificamos que nuestra aplicación requiere una pureza ISO 8573-1 [1: 2: 3] significará que:
- Necesitamos que por metro cúbico de aire comprimido haya menos de 20.000 partículas sólidas de diámetro entre 0,1 y 0,5 micras, menos de 400 entre 0,5 y 1 micras y menos de 10 partículas de entre 1 y 5 micras.
- Respecto al agua, el punto de rocío a presión debe ser inferior a -40ºC.
- Y con el aceite, menos de 1mg por metro cúbico.
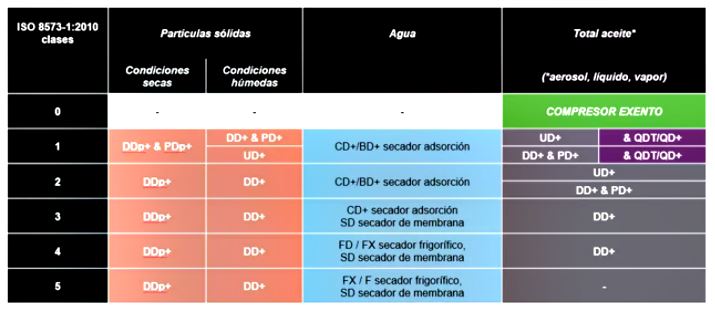
PUNTOS DE MUESTREO Y FRECUENCIA
Una sola muestra una vez al año no representa adecuadamente la salud y la calidad del sistema de aire comprimido, se debe hacer con una frecuencia basada en un análisis de riesgos.
Recordar que también las pruebas antes y después del mantenimiento ayudan a garantizar que todo el mantenimiento programado y los protocolos son adecuados y funcionan como se espera.
Autora:
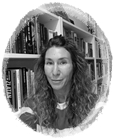
Leila Burin.
Coordinadora Académica de Portal de Inocuidad.
PhD en Ciencias Químicas, Universidad de Buenos Aires, 2001 y Lic. en Ciencias Biológicas, Universidad de Buenos Aires, 1994.
2010 hasta la fecha: auditora para SAI Global Spain: Esquemas: IFS, BRC, ISO 22 000, FSSC 22000, GMA SAFE y auditorías de clientes: Unilever, Pepsi, Starbucks, Woolworths, Mac Donalds.
1997 hasta la fecha: QualyFoods S.A., Argentina Cargo: Gerencia Técnica en Aseguramiento de Calidad. Dirección. Desarrollo de Programas de Pre-requisitos & BPM y HACCP en Argentina (8 Plantas); capacitación: HACCP Alliance Lead Instructor en Argentina y México; y auditora para Heinz NA.
Mas de 15 cursos abiertos dictados desde 2001. Docencia: Materia: Biología e Introducción a la Biología Celular. Unidad Académica: CBC (Ciclo Básico Común), UBA, entre 1993 y 2000.
2 DIRECCIONES DE TESIS, entre 2001 y 2006.
14 PUBLICACIONES Y ARTÍCULOS.
18 TRABAJOS PRESENTADOS A CONGRESOS.
Más de 35 CURSOS TOMADOS desde 1994.
Portal de Inocuidad © Se prohíbe la reproducción total o parcial de los contenidos sin citar su fuente o solicitar autorización.
Aquí pueden dejarnos sus comentarios